A Conical Mixing Tank is a specially designed vessel used for blending, mixing, and sometimes even storing liquids or slurries in various industries. As the name suggests, its most defining feature is its cone-shaped bottom, which differentiates it from flat-bottom tanks. This unique design not only aids in thorough mixing but also allows for efficient discharge and easy cleaning. These tanks are often found in sectors such as chemical manufacturing, food and beverage processing, pharmaceuticals, cosmetics, water treatment, and agriculture.
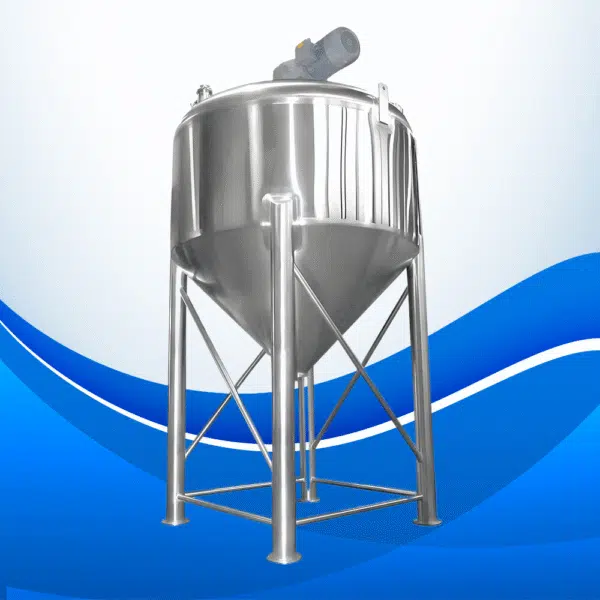
The primary purpose of a conical mixing tank is to provide consistent and homogeneous mixing of materials. Whether you are blending two liquids, suspending solids in a liquid, or dissolving powders into a solution, a conical tank can significantly enhance the mixing performance due to its geometry and the type of mixing equipment integrated with it.
Design and Structure of a Conical Mixing Tank
The tank is typically constructed from durable materials like stainless steel, polyethylene, or polypropylene, depending on the application and the type of substances being handled. The conical shape refers to the bottom section of the tank, which slopes downward to a single outlet point. This design ensures that the contents naturally flow downward, aiding in full drainage and minimizing product waste.
The top part of the tank can be either open or closed, and may include features such as manways, lids, or ports for introducing materials or inserting sensors. Internally, the tank may be fitted with agitators, paddles, or other mixing elements, often powered by a motor located on the top or side of the vessel. These mixing devices are responsible for generating the movement needed to combine the ingredients effectively.
How the Mixing Process Works
The mixing process inside a conical tank begins when the agitator or mixer is activated. The impellers start to rotate, creating a vortex or flow pattern that draws materials from the top down to the cone and then back up again along the sides. This cyclical movement ensures that every part of the tank’s contents is consistently mixed.
The conical bottom plays a crucial role in this mechanism. It prevents dead zones, which are areas where the fluid remains stagnant and does not get mixed. By directing materials toward the center and downward, the conical base enhances circulation and helps integrate all ingredients more uniformly.
The steep angle of the cone also helps heavier particles settle to the bottom, where they can be resuspended by the mixing blades or easily removed through the discharge valve. This makes conical tanks particularly useful when working with suspensions or ingredients with different densities.
Advantages of Using a Conical Mixing Tank
One of the most important advantages of conical mixing tanks is their efficient drainage. When the tank is emptied, the cone-shaped base ensures that little to no product is left behind, reducing waste and making cleaning much easier. This is especially important in food, pharmaceutical, and cosmetic applications where hygiene and material integrity are vital.
Another benefit is the improved mixing efficiency. Because of the conical design and the strategic placement of the mixing equipment, the contents are mixed more thoroughly and quickly compared to flat-bottom tanks. This leads to time savings and better product consistency.
Additionally, these tanks can be customized with heating or cooling jackets to control the temperature during mixing, which is essential for many chemical or biochemical processes. The conical design also allows for a modular setup, making it easier to scale operations up or down depending on production needs.
Common Applications Across Industries
Conical mixing tanks are used in a wide range of industries for various purposes. In the food and beverage sector, they are employed to blend ingredients like syrups, sauces, dairy products, and juices. In pharmaceuticals, they help mix active ingredients with excipients to create consistent drug formulations.
In the chemical industry, these tanks handle reactions that require thorough mixing under controlled conditions. For agriculture and fertilizer production, they aid in the preparation of nutrient solutions or pesticide blends. Even in water treatment facilities, conical tanks are used for mixing chemicals needed to purify water.
Each industry has specific requirements, and conical tanks can be adapted accordingly. Whether it’s pressure resistance, corrosion resistance, or compliance with sanitary standards, the tank can be engineered to meet the exact demands of the application.
Maintenance and Operational Considerations
To ensure the long-term performance of a conical mixing tank, regular maintenance is essential. This includes inspecting the agitators and seals, checking for wear or corrosion, and keeping the tank clean to avoid contamination. The discharge valve should also be maintained to prevent clogging or leakage.
Operators should be trained on proper use, including how to control the mixing speed, monitor temperature if applicable, and safely add ingredients. Automated systems with sensors and control panels can help optimize the mixing process and reduce human error.
Choosing the right size, material, and configuration is also important to get the best results. Consulting with a manufacturer or engineer can help determine the optimal setup for your specific needs.
Conclusion
A conical mixing tank is a versatile and efficient solution for blending liquids and solids across various industries. Its unique design offers benefits in terms of drainage, mixing performance, and ease of cleaning, making it a valuable asset in production processes. Whether you’re working in food, pharmaceuticals, chemicals, or any other sector that requires precise and uniform mixing, a conical tank can help ensure high-quality outcomes with improved operational efficiency. Understanding how it works and how to maintain it properly can go a long way in maximizing its usefulness and longevity.